- Quality control has evolved from artisanal methods to technology-driven processes, significantly enhancing efficiency and scalability.
- Advances in AI, IoT, and QC tools have set higher benchmarks in IT and other industries, improving product quality and customer satisfaction.
- Continuous training and teamwork are crucial for effective quality control, fostering innovation and ensuring adherence to industry standards.
Did you know that quality control, which once relied on artisanal methods, has evolved into sophisticated, technology-driven processes? The journey of quality control began in the ancient world, where craftsmanship was the cornerstone of quality. Artisans, revered for their skills, took immense pride in their work. Each product was meticulously crafted, and the artisan’s reputation hinged on the quality of their output. This personalized approach ensured high-quality outputs but needed to be more scalable. Today, products such as pottery, textiles, and metalwork are inspected using cutting-edge technologies like AI and IoT, a far cry from the individual inspections of the past.
It was the 18th century, towards the end of it, to be precise, when the prospects of quality control gathered some momentum. Thus, the increase in industrial production saw the need for more structured approaches to QC. Inspection and sorting started to be posted in factories to prevent unreliable products. The first systematic approaches of QC and the means of standardized production can be attributed to this period. However, these early methods were still rudimentary; the inspection process was often done manually and was time-consuming.
The first significant leap in QC’s evolution occurred in the 1920s, with the introduction of an approach called ‘statistical quality control’ by Walter A. Shewhart. This was a significant change that focused on the application of statistical tools to measure and regulate quality within production. It shifted from merely inspecting items at the end of the line, where the problem could only be found and not solved, to a proactive approach that prevented defects instead of just detecting them. This was a pivotal moment in the history of QC, enlightening us about the power of statistical tools in maintaining quality.
The third major landmark in the evolution of quality control was attained in the post-World War II period when W. Edwards Deming played a pivotal role in propagating quality management principles to Japanese manufacturers. Out of Deming’s approaches that focused on daily improvement and the proper effects, radical product quality and reliability improvement were achieved. His teachings also set the stage for what is now called Total Quality Management (TQM), but more importantly for the Japanese manufacturing society, where quality became an essential trademark of made-in-Japan products.
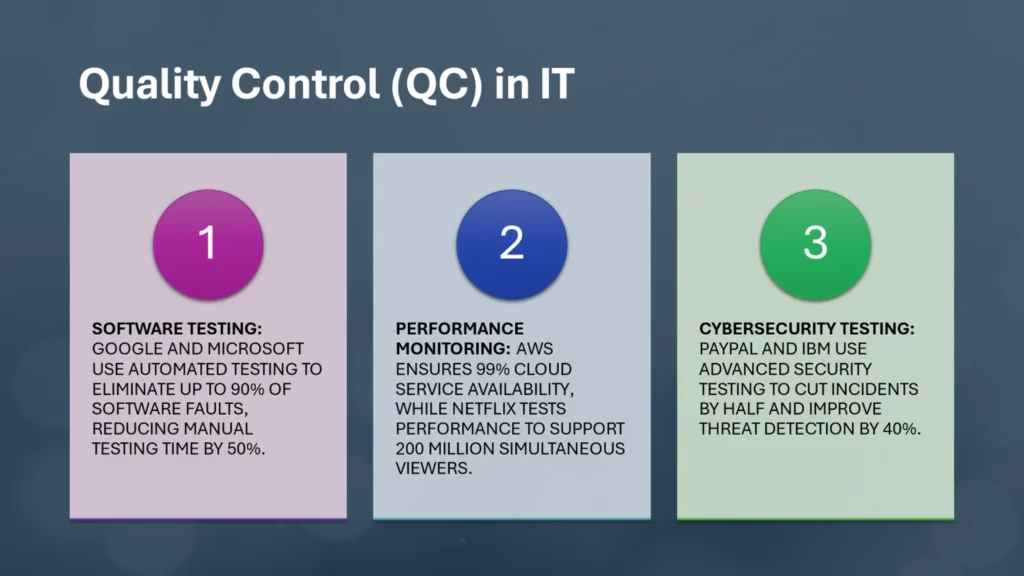
Quality Control (QC) in Information Technology (IT)
QC is valuable and essential for software, systems, and IT services in information technology. Recent statistics highlight its importance: It has also been found that corporations that apply extensive QC measures get to enjoy up to 30% fewer software defects, a 40% earlier time to market new products, and a 50% lesser number of post-release bugs. Also, organizations with highly efficient QC systems have noted an increased customer satisfaction level of 25%. Organizations are now using sophisticated approaches to QC to develop very sound IT solutions; hence, the quality and satisfaction of consumers are enhanced.
Software Testing: Ensuring applications stay reliable requires efficient software testing. Google also employs unit, integration, and acceptance testing when deploying the corporation’s software. This process erases most software faults, which can take up to 90%. Automated testing tools like Visual Studio Test are applied at Microsoft; here, firms can reduce time spent on manual testing by 50% while testing coverage has been raised by 40%.
Performance Monitoring: Performance management confirms that the IT services are running at their best. Amazon Web Services (AWS) utilizes performance monitoring instruments like CloudWatch, and through CloudWatch, AWS has glassed a 99. cloud services availability of 99% at the firm. Netflix also runs performance tests to see how many viewers can stream simultaneously, specifically up to 200 million, with little to no lag on the site.
Cybersecurity Testing: Cybersecurity testing for cyberspace is crucial for threat prevention. Security testing comprises vulnerability scanning and penetration testing, helping PayPal cut its security-related incidence by half to boost its protection from cyber risks. IBM also uses high-quality threat detection technology, increasing the threat & security recognition rate by up to 40% for its cloud services and enterprise solutions. With these improvements in advanced QC methods, many companies, such as Google, AWS, Netflix, PayPal, and IBM, have raised quality and performance benchmarks for the IT industry. Their strategies contribute to increasing operational performance and producing better-quality goods and services, thereby illustrating the role of technology in QC.
Technological Advancements in Quality Control (QC)
Recent developments have improved QC by a significant percentage, employing the involvement of new technological methods. For instance, using AI and ML technologies may result in enhanced defect detection rates, which are 30% higher than the standard approach. Using IoT to maintain real-time monitoring can help reduce production loss by up to 20 percent in industries. Here’s a detailed look at how leading companies are harnessing these advancements:
Artificial Intelligence (AI) and Machine Learning (ML): These acronyms, AI and ML, transform QC by predicting defects and facilitating more efficiency. Operations have incorporated predictive maintenance features that utilize AI; the company’s maintenance costs have since been slashed by 10%, while equipment downtime has decreased by 15%. Image recognition systems control the quality of iPhone components, Increasing the work’s efficiency by 25% due to the prompt identification of defects. These AI systems work with speeds of image processing, which range between thousands of images per second, and the images are usually analyzed for detection of defects.
Internet of Things (IoT): Thus, IoT enhances the real-time detection and management of events. Today, GE, for example, has managed to cut its maintenance costs by a third and boost equipment productivity by a quarter using IoT sensors in its industrial equipment. Digital wind farms by GE IoT sensors increase the capacity of efficient working of new turbines and increase energy production by 15%. Bosch has embraced the IoT of automotive output, where they use the devices to make instant adjustments hence enhancing the quality by 20%.
Advanced QC Tools: Devices like AOI and NDT are improving product qualities and QC capability. AOI systems have been applied in Samsung’s semiconductor manufacturing, which has helped to drop defect rates by 35% and boost yield rates tremendously. Boeing utilizes techniques such as ultrasonic and radiographic testing, such as NDT that provide up to 40% better detection of internal faults in aerospace products to guarantee that the aerospace parts and structures are safe and dependable.
Stories of QC Professionals
Behind every quality control (QC) process are dedicated professionals who work tirelessly to ensure standards are met and maintained. These individuals play a critical role in the success of QC systems, bringing their expertise, dedication, and collaborative spirit to the forefront. Understanding the human aspect of QC helps to appreciate the daily challenges and triumphs these professionals face and underscores the importance of ongoing training and teamwork. The Story of Farooq Zafar – Quality Control Specialist for Fortray’s Educational Programs
“Hi, I’m Farooq Zafar, and I manage quality control at Fortray’s educational programs division. My role is to ensure that all our courses and training materials meet the highest standards of quality and relevance. Each day, I start by reviewing feedback from our students and trainers, which is crucial for identifying areas for improvement and updating our materials accordingly. Developing a new feedback system was one of the most rewarding projects I’ve worked on. Previously, collecting and analyzing student feedback was cumbersome, often delayed, and lacking detailed insights. I led the initiative to design and implement a streamlined, user-friendly feedback system. This new system allowed us to gather real-time data and swiftly adjust our courses based on student input.
The impact was remarkable. We saw a significant enhancement in the quality of our courses, and student satisfaction and engagement increased notably. Witnessing how my efforts directly improved our students’ learning experiences was incredibly fulfilling. Projects like these remind me why I am passionate about ensuring quality in educational programs.” Javeria’s Story: Customer Service Excellence in Managed IT Services
“Hello, I’m Javeria, a senior customer service manager in Fortray’s managed IT services division. My role is to ensure that our clients receive exceptional support and that their IT needs are met with efficiency and expertise.
One of the most challenging and rewarding projects I have led involved addressing a major client’s IT service issues. This large organization was experiencing frequent downtime and persistent security concerns, severely affecting its operations. I spearheaded a team to enhance our customer support processes, implementing new communication protocols and a comprehensive troubleshooting system.
We faced tight deadlines and numerous technical obstacles. However, through careful planning and teamwork, we successfully addressed the client’s issues on schedule. We introduced advanced support techniques, including proactive issue resolution and regular performance reviews, significantly improving the client’s experience. The client was delighted with the outcome, noting a substantial reduction in downtime and no further security issues.
This project’s success underscored the critical role of quality customer service in IT. Knowing that our efforts directly contributed to the client’s satisfaction and operational stability was incredibly rewarding. Moments like these highlight the profound impact of exceptional customer support in managed IT services.”
Training and Teamwork
“Emphasizing the importance of ongoing training and a culture of teamwork highlights how these elements contribute to effective QC.
QC is never a one-person show; it takes a team of efficient workers to produce good results. QC professionals are updated with new standards, technologies, and methodologies through continuous training. For example, Fortray provides specific courses that focus on some areas or fields of QC and equip the working people with the means and information they require for their jobs. These courses focus on state-of-the-art strategies, enabling the QC teams to address the various challenges of contemporary QC processes. Teamwork is also essential in QC. Working in teams promotes information sharing, problem-solving, and shared responsibility for quality. Another advantage of a typical QC team is that each member contributes their strengths and, therefore, comes up with a holistic perception of the issue. Team meetings, training, and projects enable people to become a single team that can handle quality issues.
For instance, once, when my team and I were working at Fortray’s division of educational services, we required a fresh industry regulation to be incorporated into training methodologies. It was a hectic schedule, and there was pressure because time was a critical factor. Thus, leveraging our diversity, we quickly implemented change across the closely connected teams to make the changes and adhere to the policies while not impairing course quality. What I appreciated the most was the feeling of togetherness I underwent during those few weeks of exam preparation. To facilitate our work, we used daily meetings to discuss the status and determine how to overcome our problems. It helped meet the set deadline, developed a much-needed team spirit, and enhanced efficiency for future undertakings. Likewise, other subordinates like Javeria’s team in the managed IT services division are often in a similar team to solve intricate client problems.
Conclusion
One should note the necessity of humane factors in implementing QC systems. All the stories, including Farooq’s and Javeria’s professional commencement, portray that many dedicated employees of QC address the issues at hand to the best of their potential. In the case of praising, the focus on the constant training of employees and the strong culture of teamwork will demonstrate how these elements contribute to efficient QC and creating services of high quality. The quality control departments or groups thus employed act to provide positive results to organizations that invest in the development and collaboration with their quality control teams to deliver quality goods and services that would increase customer trust and satisfaction.