- Six Sigma drives operational excellence by reducing defects and improving process efficiency, leading to substantial cost savings and enhanced productivity.
- The methodology, rooted in statistical principles, ensures near-perfect quality with fewer than 3.4 defects per million opportunities, significantly impacting organizational performance.
- Lean Six Sigma certification is a career game-changer, offering professionals leadership opportunities, higher salaries, and the ability to drive transformative changes in various industries.
Imagine a world where businesses operate at peak efficiency, waste is a thing of the past, and productivity reaches new heights. This isn’t a distant dream; it’s the reality for companies embracing Six Sigma. Six Sigma is a game-changing methodology that has revolutionized various industries by driving operational excellence and boosting productivity. The term’ Six Sigma’ refers to a statistical concept. It signifies a process that produces fewer than 3.4 defects per million opportunities, ensuring near-perfect quality. The financial benefits are substantial, companies that have implemented Six Sigma report significant savings. For example, General Electric saved an estimated $12 billion over five years through Six Sigma initiatives.
The Birth of Six Sigma
It was in 1987 when Six Sigma was beginning to be developed and introduced in the industry. Thus, Six Sigma can be traced back to the early 1980s at Motorola; this electronics manufacturing firm suffered from several quality issues. At this time, Motorola was struggling with a high level of new product failures within the consumption cycle, thus damaging customer relations and hindering production rates. The organizational leaders realized an optimistic ranging application method essential to elevate the company’s quality and efficiency. Indeed, Six Sigma proved to be the answer, significantly improving the quality and efficiency of companies that embraced it.
Based on the previous study, Six Sigma was introduced by Bill Smith, often referred to as the ‘father of Six Sigma,’ and Mikel Harry. The Six Sigma methodology was developed by Bill Smith, a Motorola engineer, to solve Motorola’s vital problematic areas with quality. He favored the method of quantification of the quality and utilizing statistical tools to control and find ways of eradicating all the causes of variation. Mikel Harry, a Motorola engineer and later a very active Six Sigma consultant, was also one of the essential contributors to the development of Six Sigma as an organized process.
Mikel Harry, a Motorola engineer and later a very active Six Sigma consultant, was one of the essential contributors to the development of Six Sigma as an organized process. His engagements involved defining the process, designing the training methodology, and supporting institutions adopting Six Sigma. His dedication and expertise have significantly shaped the Six Sigma we know today, and we owe much respect to his contributions.
Methodology and Focus
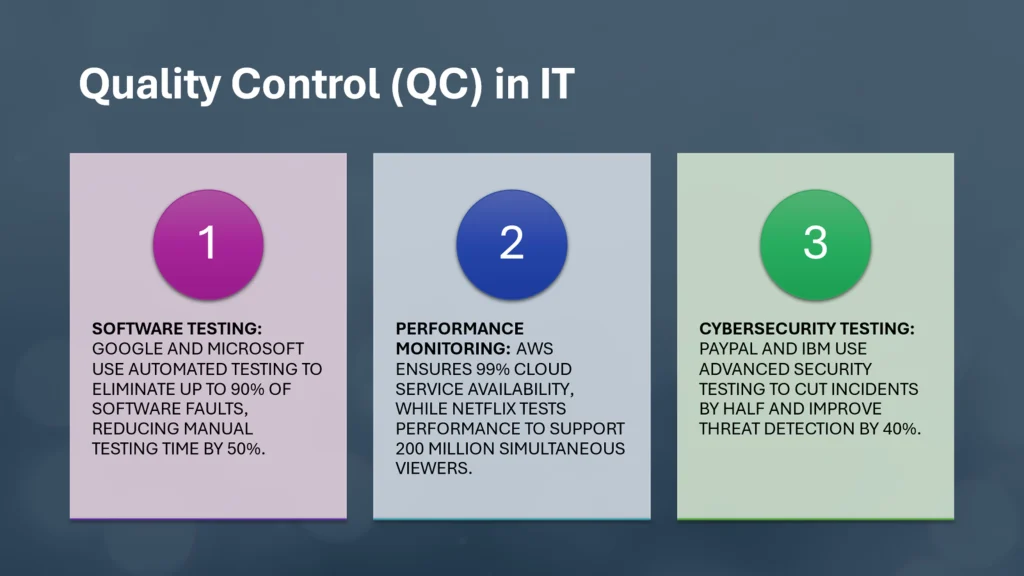
Six Sigma is a business management strategy developed to enhance quality and decrease the variation in business processes and their results while reducing defective products and services. Six Sigma” refers to the statistical concept where a process operates with a defect rate of fewer than 3.4 defects per million opportunities. The goal is to achieve near-perfect quality by focusing on the following fundamental principles:
- Define: This step states the customer’s scope, objectives, and expectations. The customer’s needs are assessed, and probable enhancement goals are determined.
- Measure: Gather information about the existing processes to build the current state snapshot. In this phase, the key performance indicators are determined, and the process performance is evaluated to analyze the current problems and deviations.
- Analyze: The principal cause of defects must be determined by analyzing the company’s acquired data. This phase involves employing statistical tools and procedures to identify the root causes of quality issues.
- Improve: Propose appropriate interventions for the causes envisaged during the analysis stage. This phase is mainly concerned with designing experiments and evaluating modifications to increase reliability and decrease abnormality.
- Control: The improved processes must be monitored and controlled to sustain these results. This phase is focused on implementing procedures and controls that can enhance the sustainment of improvements and eradicate the return of defects.
Impact and Benefits
The Six Sigma program smoothly unveiled at Motorola ensured the enhanced quality of products and, at the same time, made working operations more effective. The elimination/minimization of the defects/variability extended customer satisfaction, lower costs arising from rework/scrap, and increased Motorola’s productivity. Thus, the positive results of Six Sigma at Motorola motivated other organizations to adopt it into their business. Therefore, Six Sigma’s influence did not stop with Motorola: it contributed to developing other methodologies and quality improvement frameworks. Its principles and practices have been widely adopted. They are now recognized as part of the basis of modern concepts and approaches to quality management and continuous improvement.
As Motorola’s implementation of Six Sigma achieved remarkable results, it became widely recognized as one of the major frameworks for improving organizational performance. Since then, Six Sigma has become popular in manufacturing industries and later spread to the healthcare, finance, and sectors that provide services. Six Sigma has thus been accepted as a business strategy tool by many organizations to enhance and realize operational efficiency. It is necessary to state that Six Sigma management originated in Motorola and was motivated by quality problems and controlling the process. The methodology invented by Bill Smith and Mikel Harry has gone a long way to become one of the fundamental approaches to managing quality and improvement, bringing tangible values to organizations worldwide.
Six Sigma’s heart is the DMAIC framework—Define, Measure, Analyze, Improve, and Control. This systematic, data-driven approach helps organizations understand their processes, identify inefficiencies, and implement lasting improvements. The results speak for themselves. Motorola saved billions of dollars, and General Electric, another early adopter, reported savings of over $300 million in the first year alone.
Six Sigma in IT
The IT industry is largely fast-paced and ever-changing; managing the industry’s diverse and complex issues needs a tighter problem-solving method. Six Sigma can solve these challenges as a tool that can help optimize the software development life cycles, decrease the number of bugs in made programs, and advance project management. For example, a large IT company, which constantly faced problems with software development inconsistencies, started applying Six Sigma methodologies and got outstanding results. With the help of implementing the DMAIC method, the main reasons for the delays and defects were defined. Through the auditing and optimization of data, they cut the bug rates in half and minimized the time-to-market of new software releases. Furthermore, it can be realized that Six Sigma contributed to centralizing project management techniques, which are more likely to increase reliability regarding the results they bring. Encouraging the IT teams to look for the elimination of defects, Six Sigma’s documented and structured methodology promotes a culture of ongoing improvement. Consequently, the firm’s efficiency increased, and customer satisfaction was higher due to delivering high-quality software on time. The survey insists that IT workers using Six Sigma see improvements in their project performance, higher efficiency, and more defined methodology in solving technical problems, confirming Six Sigma’s strong standing as an essential tool in the IT field. Six Sigma, Industrial trends and success stories of recent times
AI and Machine Learning Integration at General Electric:
GE completely transformed its operations by combining both concepts. GE also adopted Six Sigma from its former CEO, Jack Welch, and has now evolved to AI Six Sigma, especially applying the jet engine’s predictive maintenance. While capturing thousands of data from sensors, the company can predict problems before they occur. At this moment, the company decreased its failure rate by thirty percent, besides lowering maintenance costs. This makes the company reliable and adds to customer satisfaction, thus promoting efficiency in flight operations.
Digital Transformation at Honeywell: Many of Honeywell’s digital transformation initiatives complement Six Sigma operations, making significant impacts. Chief executive officer Darius Adamczyk led the charge regarding cloud-based solutions and big data analytics. These tools have enabled people across the globe to collaborate, compress project cycles by a quarter, and substantiate numerical assumptions. Some notable accomplishments include the following: supply chain operation improvements, whereby we reduced the inventory cost by 15% and delivery time by 20%, proving the efficient operation of the business.
Lean Six Sigma 4.0 at Siemens:
Siemens has taken Lean Six Sigma notches higher with Lean Six Sigma 4. 0 for incorporating IoT and big data in the firm’s operations. Through smart manufacturing, chairperson Roland Busch was at the forefront, spearheading the enhancement of production lines through IoT gadgets. On this account, it has reduced the production defects by 40% and raised OEE by 30%. The efficiency by which Siemens’ solves production problems further puts it at a vantage position as a foremost manufacturing firm.
Sustainability and Green Six Sigma at Toyota:
After that, Toyota developed a new concept called Green Six Sigma, built from lean manufacturing and focused on sustainability. This was also supported by the current president, Akio Toyoda, as a way of reducing harm to the environment. Yet, for instance, such Green Six Sigma initiatives helped Toyota propel Akio Toyoda as a way of reducing damage to address the problem of waste: by the company’s estimate, the participation in Green Six Sigma projects enabled it to cut the volume of waste by a quarter and the level of carbon emissions – by a fifth at manufacturing sites. Interestingly, merely redesigning the painting process reduced the VOC emissions by half, demonstrating Toyota’s environmental consciousness and frugality.
Six Sigma in IT at IBM:
Other janitorial practices that IBM has used in IT improvement through employing Six Sigma include improving software development and project management. That was under the reign of the current CEO of IBM, Arvind Krishna, and where Six Sigma corrected ineffective methods in software development. Adopting the DMAIC methodology enabled the ferment cost of bug rates to be cut by 50% and the introduction of new software to 30% quicker. These improvements have helped to improve the quality of its products and the satisfaction of its users, thus strengthening its position as a technological firm.
Six Sigma at Ford Motor Company:
Ford Motor Company also uses Six Sigma to achieve quality and cost objectives. Information sharing showed that Six Sigma is used to improve competitiveness; for instance, Six Sigma was described by CEO Jim Farley. Because of the rationalization that has been done and the emphasis on decision-making based on data, there was a 20% decline in vehicle defects and a 25% decline in warranty claims. One significant project enhanced the concept of the assembly line of the Ford F-150 and reduced the timeline by 15%, thus enriching the production rate. These improvements have boosted Ford’s revenues, profits, and brand image.
Fortray’s Six Sigma Success Story
Six Sigma has been incorporated into the organization by Fortray, led by Chief Executive Officer Mazhar Minhas, to increase the educational programs and the organization’s quality. Facing the problem of an increase in the program’s effectiveness and a decrease in the administrative load, Minh has promoted the use of Six Sigma tools. As a result, the company applied DMAIC (Define, Measure, Analyze, Improve, Control) at Fortray to optimize the course delivery and student support systems. This proved a good strategy, increasing program completion rates by 25% and student satisfaction scores by 20%. In the same regard, operations efficiencies were also realized with an improvement in administrative overhead costs by fifteen percent. These achievements further affirmed the company’s position as one of the premier educational solutions providers and established evidence of Six Sigma in enhancing the effectiveness of educational service delivery. These success stories attested to the effectiveness of Six Sigma for organizational change across different fields. They flagged benefits such as embracing AI, transforming digital, Lean, Six Sigma 4. 0, and sustainability; leading companies, including GE, Honeywell, Siemens, Toyota, IBM, Ford, and Fortray, have realized numerous avenues to operational efficiency, cost reduction, and product quality, thus satisfying customers and enjoying competitiveness in the market. Lean Six Sigma Certification: This was indeed a career game-changer. The Lean Six Sigma certification is gaining popularity in the world of employment. Fortray is a firm that embraces this trend by providing excellent training and certification services. This certification impacts the professional with skills to lead significant changes and achieve excellent processes. All indicated that Fortray’s programs focus on delivering both theoretical and pragmatic skills in Lean Six Sigma projects’ operations. Certified professionals tend to be placed in positions of authority that attract better pay and work on sensitive projects. Apart from the noticeable improvements in efficiency and productivity, Lean Six Sigma certification has helped many, including Fortray’s graduates, to progress to significant roles in different sectors. Real-life experiences with the certification further prove the effectiveness of Fortray’s offering by demonstrating how it has helped certification holders in their quest to drive processes of positive change in their organizations and advance their careers while contributing positively to the bottom line.
Conclusion
Six Sigma’s transformative power spans industries, driving operational excellence and boosting productivity. It has proven worth, from manufacturing floors to hospital halls, financial institutions, and IT firms. For professionals, Lean Six Sigma certification offers career advancement and leadership opportunities. The future of Six Sigma looks bright, with technological innovations paving the way for even greater efficiencies. Businesses and professionals should embrace Six Sigma, stepping into a future where operational excellence is the norm and inefficiency is a thing of the past.
FAQ
Value Stream Mapping
FMEA
Pareto Chart
Histogram
The 5 Whys
Fishbone Diagram
Kanban
Kaizen
At the project level, there are master black belts, black belts, green belts, yellow belts, and white belts.
It is used to improve the organization’s products, services, and processes across various disciplines, including production, product development, marketing, sales, finance, and administration.